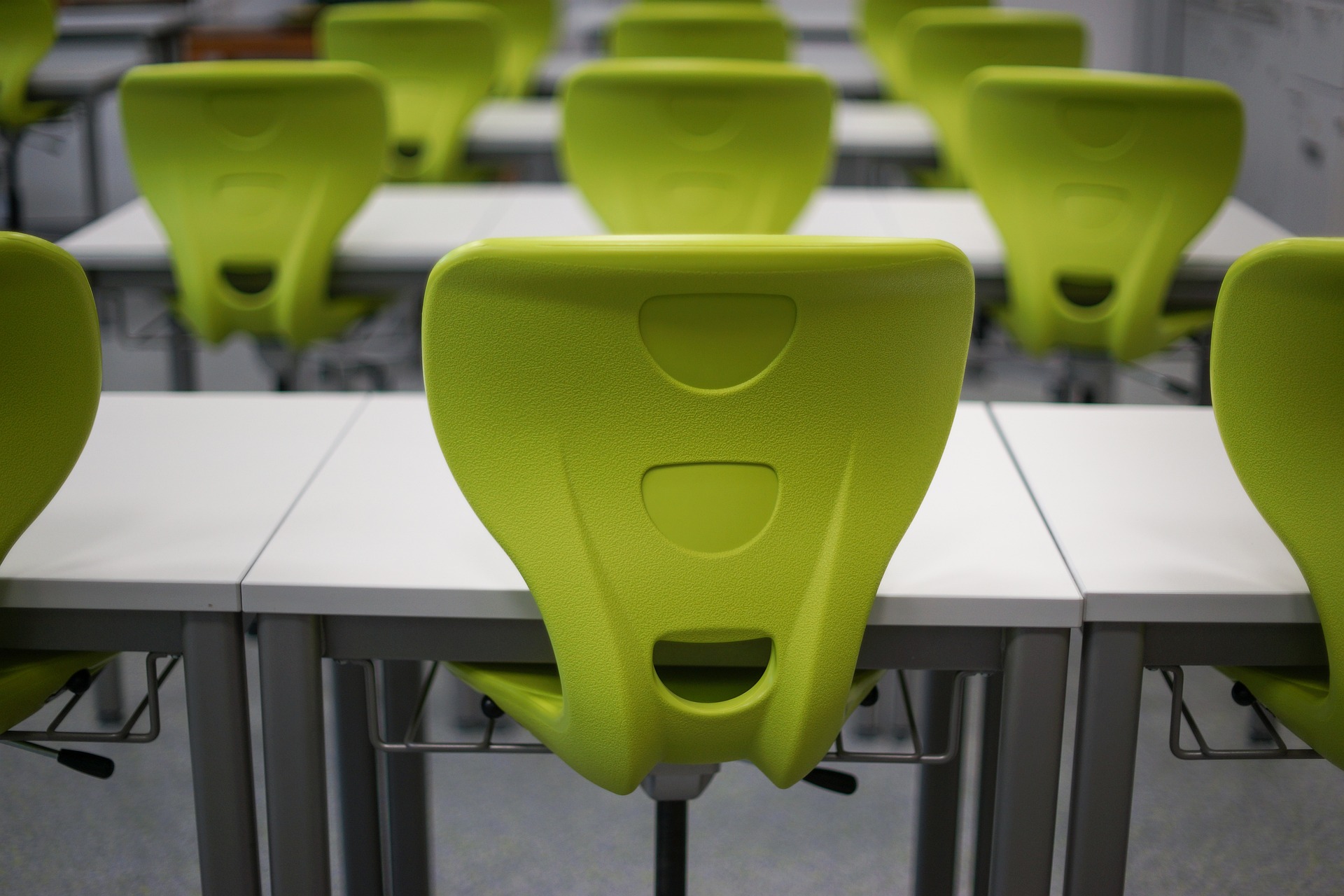
Gas-assisted Injection Molding
If you’re familiar with injection molding, you know that it’s a versatile manufacturing process that can be used to create a wide variety of products. But did you know that there’s a variation of this process that’s even more versatile? It’s called gas-assisted injection molding, and it opens a whole new world of possibilities for manufacturers. In this blog post, we’ll take a closer look at how gas-assisted injection molding works and some of the benefits it offers.
What is Gas-assisted Injection Molding?
Gas-assisted injection molding is a low-pressure process that uses pressurized nitrogen gas to help form hollow sections in thicker areas of a mold. By displacing the material in these areas, the gas helps to create a more even distribution of the material throughout the mold. This can be especially helpful in creating parts with complex shapes or intricate details.
How Does it Work?
For gas-assisted injection molding to work, the nitrogen gas must be injected into the interior of the mold at low pressure. The gas then flows through strategically placed channels within the mold. These channels help to distribute the gas evenly throughout the mold and ensure that it meets all the material. As the gas connects with the material, it displaces it and forms hollow sections. This process continues until all the material has been displaced, and only hollow sections remain.
Benefits of Gas-assisted Injection Modeling
There are several benefits to using gas-assisted injection molding, including:
Improved Structural Integrity: Gas-assisted injection molding can help to improve the structural integrity of a part by forming hollow sections within it. These hollow sections can reduce weight and increase strength, making the part more durable overall.
Increased productivity: Gas-assisted injection molding can increase productivity by reducing cycle times. This is because the gas helps to displace material quickly and efficiently, allowing for shorter cycle times overall.
Improved dimensional accuracy: Gas-assisted injection molding can also help to improve dimensional accuracy by reducing warping and distortion. This is because the gas helps to distribute heat evenly throughout the part, preventing warping and distortion from occurring.
Reduced sink marks: Another advantage is that it reduces sink marks on the surface of the part. Sink marks are caused by the pressure of the molten plastic against the walls of the mold cavity. When gas is injected into the plastic, it helps to equalize the pressure, which reduces sink marks.
Conclusion
Gas-assisted injection molding is a process that is used to hollow out plastic parts. This process is done by injecting a gas into the plastic while it is being injected into the mold. The gas helps to evacuate the molten plastic from the center of the part, which leaves a hollow shell. The result is a lighter weight and stronger part. There are many advantages to using gas-assisted injection molding, such as increased dimensional accuracy and reduced sink marks.
If you’re looking for the right gases to help you with your next project, we have what you need to get the job done. Any questions regarding the types of gases we carry, cylinder sizes, delivery, or anything else, we are happy to help you out. Chat with one of our experts by calling 562-426-4017 or get a free quote online if you already know exactly what you need.