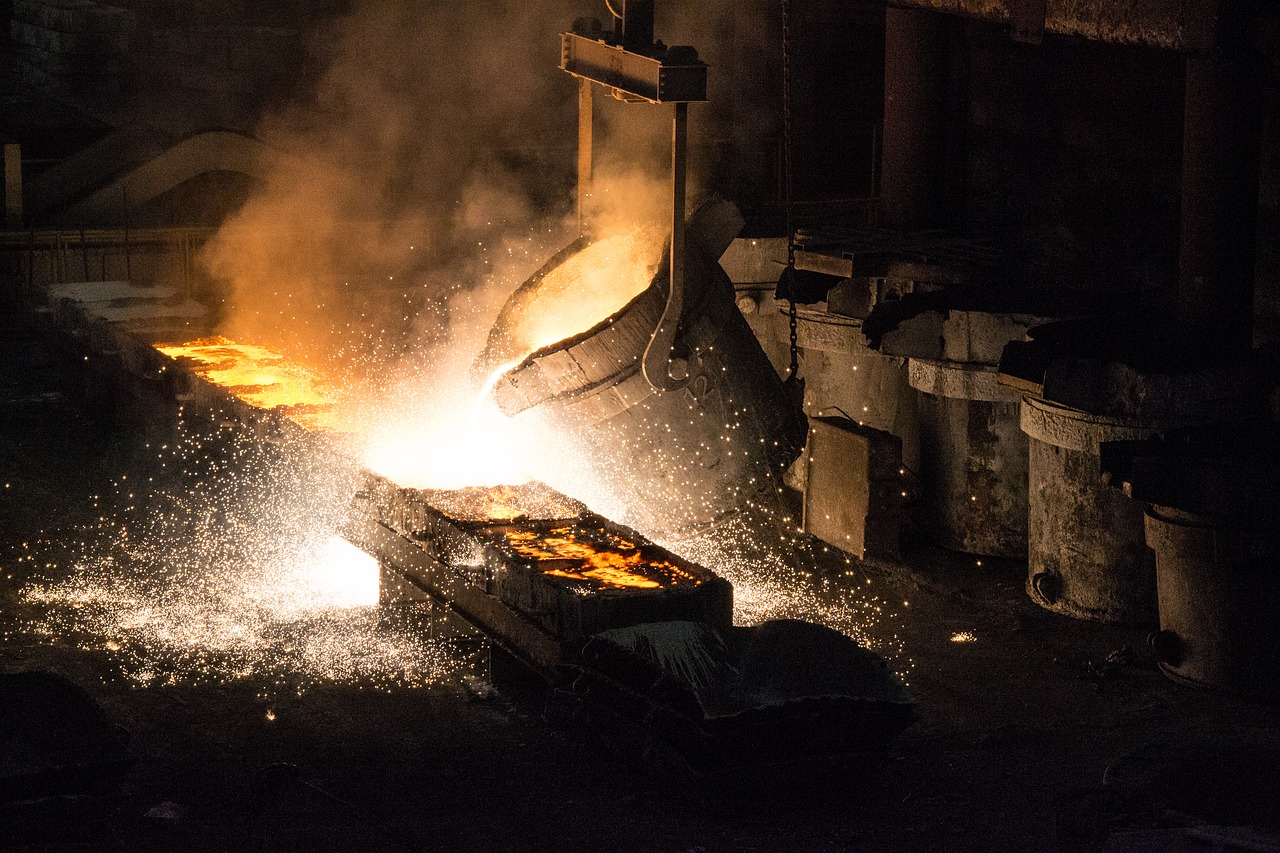
Nitrogen, Argon & Oxygen Gas Uses in Metallurgy Engineering
[vc_row row_type=”row” use_row_as_full_screen_section=”no” type=”full_width” text_align=”left” css_animation=”” box_shadow_on_row=”no”][vc_column][vc_column_text]In our previous blog post on Industrial Gases Used in the Mining Industry, we went a little into the mineral processing portion and how gases are utilized to process minerals and metals. That part of the mining process is called metallurgy.
Metallurgy is a process used to extract metals in their pure forms. It’s a method used to purify metals and turn them into alloys, which is essentially a mixture of metals. For example, silver and copper combined makes sterling silver and copper and zinc make brass.
Some of the most commonly used gases in the steel and metal industry are oxygen, nitrogen and argon. In this post, we’re going to dive a little deeper into how those gases are used and their roles in metallurgy.
Oxygen
In the steelmaking industry, oxygen is a main component in the basic oxygen process (BOP) and this process happens in a basic oxygen furnace (BOF). This process involves high purity oxygen being blown into a furnace full of molten iron and other scraps to convert it into steel.
The oxygen causes a reaction that releases heat and oxidizes impurities like carbon, for example, in the batch. Oxygen is inserted in the molten bath at super high speeds and the process lasts about 20 minutes, but can vary.
This is to reduce the amount of carbon within the steel itself thus converting hot metal into liquid steel with low carbon content. Other impurities that are abundant in the steelmaking process are sulfur and phosphorus.
Sulfur and phosphorus are typically removed by transferring them into a calcium oxide rich phase using the basic oxygen furnace. After impurities are removed, the molten steel is poured into molds to cool and ferro alloys are added to improve steel properties like strength and corrosion resistance.
Nitrogen
Nitrogen is commonly used in the annealing process of metalworking. Nitrogen annealing consists of reducing metal hardness and increasing ductility through heat treating. Annealing is an important process if you want to work with a metal that won’t crack under pressure and is easy to shape without the use of additional heat, like in cold working for example.
Annealing basically reduces the crystal structure in the metal. Metals that go through the annealing process are typically better for producing electricity. Nitrogen gas mixtures are typically used in the annealing process
Nitrogen, being an inert gas, is used to provide an inert atmosphere within the furnace during the heating and cooling process. Because oxygen blasting is used in furnaces, it creates oxidation and chemical reactions which makes nitrogen a key gas to neutralize the environment.
Before the actual annealing process, nitrogen is also used to displace any hazards in the atmosphere that could potentially cause an unstable or combustible environment.
Argon
When it comes to using argon in the steel making process, it is used in conjunction with oxygen in a process called argon oxygen decarburization (AOD). This process takes place after the metals are melted down into liquid form.
The AOD process itself goes through three stages: decarburization, reduction, and desulfurization
During the decarburization process, the liquid metal is transferred into a vessel to be further refined by injecting an argon-oxygen gas mix. The vessel is very similar to the one used in a basic oxygen furnace.
Previously, we stated that oxygen reduces the carbon content in the metals. By diluting that oxygen with argon, it lowers the pressure of oxygen and carbon monoxide and only oxidizes a small amount of alloy vs a larger portion without the presence of argon gas.
As the carbon levels drop, more argon gas is added to create a higher argon concentration. After this, argon is used to help mix and remove hydrogen and nitrogen elements.
Then, in the reduction and desulfurization stages, alloys, lime and fluorspar are added to help manage the slag, which is a by-product that is formed during this process. It is sometimes used in concrete or as an added material to produce roads.
Additional elements are added in the desulfurization stage to dilute sulfur and remove oxygen. After required sulfur levels are reached, the slag by-product is removed and the vessel is then ready to be tapped and poured into molds.
Wrap Up
In the metallurgy industry, these various gases are used in several different phases of metal production from start to finish. It’s a very complex process and there are different ways to go about fabricating metals and steel.
We walked through some of the various processes within metallurgy using oxygen, nitrogen, argon and a variety of gas mixtures. If you’re in the market for industrial gases, we have what you need to get the job done.
Contact our professional at Air Source Industries for a quote and if you’re a business, make sure to ask about our next business day delivery in the LA and OC areas. We are happy to be your local gas provider. Feel free to give us a call at (562) 426-4017 if you have any questions or are looking to get a quote..
Sources:
https://www.eiga.eu/our-industry/products-and-services/metallurgy/
https://www.britannica.com/technology/basic-oxygen-process/
https://www.generon.com/nitrogen-annealing-purpose-uses/
https://thermocalc.com/showcase/application-examples/basic-oxygen-furnace-processing/
https://www.britannica.com/technology/steel/Continuous-casting/
https://en.wikipedia.org/wiki/Argon_oxygen_decarburization/[/vc_column_text][/vc_column][/vc_row]